3D Concrete Testing
Testing services for your products and materials
What is 3D Concrete Printing?
3D concrete printing is a process of using a 3D printer to create concrete structures. The printer uses a nozzle to deposit concrete in layers, which are then cured to form a solid structure. This process can be used to create a wide variety of concrete structures, including walls, columns, beams, and even entire buildings.
3D concrete printing offers a number of advantages over traditional construction methods. It is faster, more efficient, and can be used to create more complex structures. It is also more environmentally friendly, as it requires less material and produces less waste.
However, 3D concrete printing is still a relatively new technology, and there are some challenges that need to be addressed. One challenge is the cost of the printers. They are still very expensive, which limits their use to large-scale projects. Another challenge is the quality of the concrete. The concrete must be specially formulated to be 3D printable, and it can be difficult to achieve the same strength and durability as traditional concrete.
Despite these challenges, 3D concrete printing is a promising technology with the potential to revolutionize the construction industry. As the technology continues to develop, it is likely that 3D concrete printing will become more affordable and widespread.
Here are some of the benefits of using 3D concrete printing:
- Speed: 3D concrete printing can be much faster than traditional construction methods. For example, a 3D printer can print a wall in a matter of hours, while a traditional construction crew would take days or even weeks.
- Efficiency: 3D concrete printing is a very efficient use of materials. The printer only uses the amount of concrete that is needed, and there is very little waste.
- Versatility: 3D concrete printing can be used to create a wide variety of structures, including walls, columns, beams, and even entire buildings. It can also be used to create complex shapes and designs that would be difficult or impossible to create with traditional construction methods.
- Sustainability: 3D concrete printing is a more sustainable construction method than traditional methods. It requires less material and produces less waste.
Here are some of the challenges of using 3D concrete printing:
- Cost: The cost of 3D concrete printers is still relatively high, which limits their use to large-scale projects.
- Quality: The quality of 3D concrete is still being developed. It is important to use a high-quality concrete mix and to follow the proper printing procedures in order to achieve the desired strength and durability.
- Safety: 3D concrete printers can be large and complex machines, and they can pose a safety hazard if they are not operated properly.
Overall, 3D concrete printing is a promising technology with the potential to revolutionize the construction industry. As the technology continues to develop, it is likely that 3D concrete printing will become more affordable and widespread.
What is 3D Concrete Testing?
3D concrete testing is a process of evaluating the properties of concrete that has been printed using a 3D printer. This type of testing is important to ensure that the printed concrete meets the required strength, durability, and other performance criteria.
There are a variety of different 3D concrete testing methods that can be used. Some of the most common methods include:
- Compressive strength testing: This test measures the ability of the concrete to resist compression. It is one of the most important tests for evaluating the strength of concrete.
- Tensile strength testing: This test measures the ability of the concrete to resist tension. It is less common than compressive strength testing, but it can be important for evaluating the performance of concrete in certain applications, such as bridges and beams.
- Flexural strength testing: This test measures the ability of the concrete to resist bending. It is often used in conjunction with compressive strength testing to evaluate the overall performance of concrete.
- Water permeability testing: This test measures the ability of water to pass through the concrete. It is important for evaluating the durability of concrete, as water can cause corrosion and other damage.
- Abrasion testing: This test measures the ability of the concrete to resist wear and tear. It is important for evaluating the performance of concrete in applications where it will be exposed to abrasion, such as sidewalks and driveways.
3D concrete testing is an important part of ensuring the quality of concrete that has been printed using a 3D printer. By conducting regular testing, it is possible to identify any problems with the concrete and to take steps to correct them. This can help to ensure that the printed concrete meets the required strength, durability, and other performance criteria.
Here are some of the benefits of 3D concrete testing:
- Improved quality: 3D concrete testing can help to improve the quality of concrete by identifying any potential problems early on. This can help to prevent costly repairs or failures later on.
- Increased safety: 3D concrete testing can help to increase the safety of concrete structures by ensuring that they meet the required strength and durability standards.
- Reduced risk of accidents: 3D concrete testing can help to reduce the risk of accidents by identifying any potential hazards, such as weak spots in the concrete.
- Improved sustainability: 3D concrete testing can help to improve the sustainability of concrete structures by ensuring that they are designed and built to last.
Overall, 3D concrete testing is an important tool for ensuring the quality, safety, and sustainability of concrete structures.
3D Concrete Testing Plan
The following is a list of tests that are often included in testing plans for 3D printed concrete:
Property | Material | ASTM / Method | Details |
---|---|---|---|
Acceptance Criteria | 3D Printed Concrete Walls | ICC-ES AC509 | Acceptance Criteria for 3D Automated Construction Technology for 3D Concrete Walls Test criteria describes a typical test plan for evaluation of 3D printed concrete wall performance. The criteria covers the ASTM methods described below and modifications to the methods that specifically apply to 3D printed concrete. Other test methods are also described, and may be required, depending on the product beign tested. |
Compressive Strength | Concrete Cylinders | ASTM C39 | Compressive Strength of Cylinderical Concrete Specimens Molded or cored concrete specimens are tested in compression and the strength is reported on a pounds/square inch basis. |
Compressive Strength | Mortar | ASTM C109 | Compressive Strength of Hydraulic Cement Mortars Using 2″ Cube Specimens Cube specimens are cast and three are tested at each of 1, 3, 7, and 28 days of curing. Samples are cured for the first 24 hours in a standard moist room, and all subsequent days in saturated lime water. |
Consistency (Slump) | Fresh Concrete | ASTM C143 | Slump of Hydraulic Cement Concrete Performed on freshly cast material only. Wet concrete is consolidated in a calibrated “slump cone”. The cone is removed, and the consistency (slump) of the material is determined by measuring the change in height of the cone of concrete. |
Length Change | Concrete Beams | ASTM C157 | Length Change of Hardened Hydraulic-Cement Mortar and Concrete Mortar or concrete is cast into beams and cured per ASTM C157 procedures. The lengths of the beams are measured, and the beams are allowed to cure in standard conditions (either lime water or laboratory air) for a period of up to 64 weeks. Intermetent readings are taken to determine the length change of the material. |
Time of Setting | Fresh Concrete | ASTM C403 | Time of Setting of Concrete Mixtures by Penetration Resistance Performed on freshly cast material only. The coarse material in fresh concrete is removed, with the remaining material collected in an appropriate container. Material is allowed to cure, and is periodically penetrated with a calibrated concrete penetrometer. A curve of penetration resistance over time is used to calculate initial and final setting times of the material. |
Freeze Thaw Resistance (Durability Factor) | Concrete | ASTM C666 | Resistance of Concrete Beams to Rapid Freezing and Thawing. Concrete prisms are exposed to 300 cycles of rapid freezing and thawing. The fundamental transverse frequency is determined at 30 cycle intervals, and this is used to determine the durability factor rating (out of 100). |
Consistency (Slump Flow) | Self-Consolidating Concrete | ASTM C1611 | Slump Flow of Self-Consolidating Concrete Performed on freshly cast material only. Wet concrete is consolidated in a calibrated “slump cone” in either an uprigth (Procedure A) or inverted (Procedure B) manner. The mold is raised and the diameters of the resulting slumped concrete are measured at two opposite locations, and the slump flow is calculated. |
Wall Panel Strength Properties | Wall Panels | ASTM E72 | Conducting Strength Tests of Panels for Building Construction Test method describes various test orientations and loading methods for conducting standard strength tests on walls. Orientations include compressive load, tensile load, transverse load, concentrated load, impace load, and racking load. |
Flexural Bond Strength | Masonry | ASTM E518 | Flexural Bond Strength of Masonry A stack of masonry is assembled that is representative of the material being tested, and assembled per ASTM E518 instructions. The stack is then tested in either a third-point or uniform loading apparatus and loaded to faillure. The flexural bond strength is reported based on the loads attained and the specimen dimensions. |
Diagonal Tension (Shear) | Masonry Assemblages | ASTM E519 | Diagonal Tension (Shear) in Masonry Assemblages A masonry assemblage is assembled that has an area of 4’x4′. The assemblage is appropriately attached to the shear load test frame and two opposite corners are loaded in compression. Shear stress is reported based on the loads attained and the specimen dimensions. Optionally, shear strain may be reported by instrumenting the assemblage with length measuring devices. |
3D Concrete Testing Standards
Standards and acceptance criteria related to 3D concrete testing:
- ICC-ES AC15 – Acceptance Criteria for Concrete Floor, Roof and Wall Systems and Concrete Masonry Wall Systems
- ICC-ES AC509 – Acceptance Criteria for 3D Automated Construction Technology for 3D Concrete Walls
- ACI 318 – Building Code Requirements for Structural Concrete
- ASTM C31 – Making and Curing Concrete Test Specimens in the Field
- ASTM C33 – Concrete Aggregates
- ASTM C39 – Compressive Strength of Cylindrical Concrete Specimens
- ASTM C109 – Compressive Strength of Hydraulic Cement Mortars (Using 2-in. or [50-mm] Cube Specimens)
- ASTM C143 – Slump of Hydraulic-Cement Concrete
- ASTM C157 – Length Change of Hardened Hydraulic-Cement Mortar and Concrete
- ASTM C173 – Air Content of Freshly Mixed Concrete by the Volumetric Method
- ASTM C270 – Mortar for Unit Masonry
- ASTM C403 – Time of Setting of Concrete Mixtures by Penetration Resistance
- ASTM C469 – Static Modulus of Elasticity and Poisson’s Ratio of Concrete in Compression
- ASTM C494 – Chemical Admixtures for Concrete
- ASTM C496 – Splitting Tensile Strength of Cylindrical Concrete Specimens
- ASTM C567 – Determining Density of Structural Lightweight Concrete
- ASTM C666 – Resistance of Concrete to Rapid Freezing and Thawing
- ASTM C1019 – Sampling and Testing Grout for Masonry
- ASTM C1116 – Fiber-Reinforced Concrete
- ASTM C1386 – Precast Autoclaved Aerated Concrete (AAC) Wall Construction Units
- ASTM C1437 – Flow of Hydraulic Cement Mortar
- ASTM C1452 – Reinforced Autoclaved Aerated Concrete Elements
- ASTM C1583 – Tensile Strength of Concrete Surfaces and the Bond Strength or Tensile Strength of Concrete Repair and Overlay Materials by Direct Tension (Pull-off Method)
- ASTM C1611 – Slump Flow of Self-Consolidating Concrete
- ASTM E72 – Conducting Strength Tests of Panels for Building Construction
- ASTM E84 – Surface Burning Characteristics of Building Materials
- ASTM E119 – Fire Tests of Building Construction and Materials
- ASTM E455 – Static Load Testing of Framed Floor or Roof Diaphragm Constructions for Buildings
- ASTM E518 – Flexural Bond Strength of Masonry
- ASTM E519 – Diagonal Tension (Shear) in Masonry Assemblages
- UL 263 – Fire Tests of Building Construction and Materials
- UL 723 – Test for Surface Burning Characteristics of Building Materials
- UL 3401 – Outline for 3D Printed Building Construction
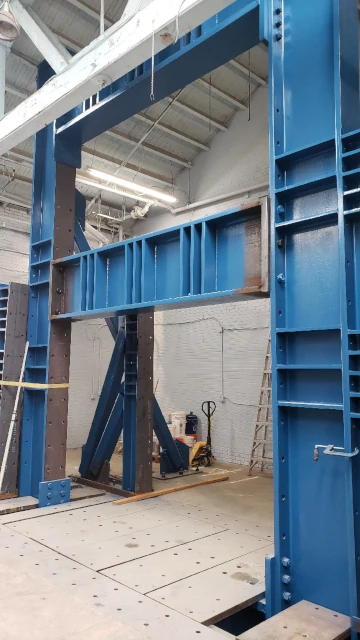
2.5-Million-pound Capacity Structural Test Frame
Axial: 2.5-million lbf axial compression
3D concrete section size: 8 ft wide x 10 ft tall
Transverse: 250,000 lbf transverse load
3D concrete section size: 12 ft wide x 10 ft tall
Racking: 250,000 lbf racking load
3D concrete section size: 8 ft wide x 10 ft tall
Please contact us for technical details and pricing.
You can view our complete listing of accredited standards and more information on testing services.